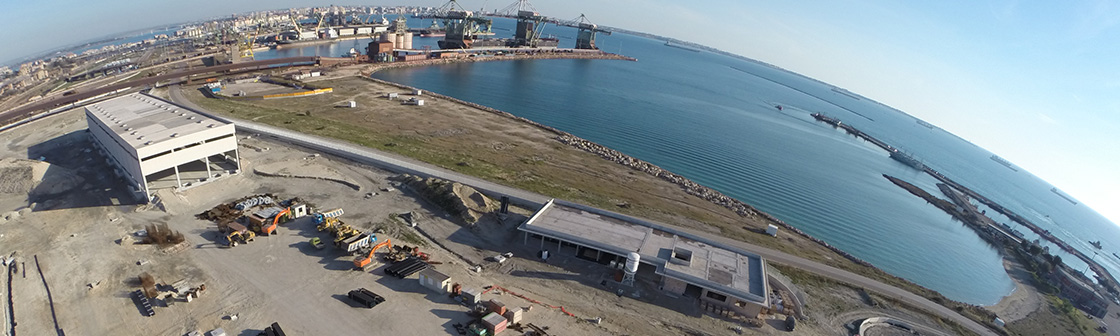
An integrated logistic platform may be considered as an exchange center between two or more transport systems (road-railway-via air) and, in regards to short and medium-long distances of the road transport system, as a infrastructure offering appropriate storage capacity and goods’ processing facilities.
Nowadays, the traffic of goods involves an international and global commerce and, therefore, the new logistic lines which are developing are characterized by velocity, quality and convenience high standards. The integrated logistic platform must be therefore located near vital airports and/or ports or near major flow exchanging points and/or near large centers of consumption.
Companies must find all possible transport services, guaranteed by specialized workers in free competition. The platform will be more efficient, the more services it will offer.
Indeed, the passage from an operator to the following (which continues a specific operation) will have a low cost if both operators work on the same platform; obviously, the platform can’t be equipped with all possible services for all kinds of goods, since the specialization on few typologies of goods, especially for the value added ones, is the basis for the success of the platform itself.
The platform’s targets are the National and Foreign Companies which work in the center and south of Italy as well as those transporting their goods in the Mediterranean Sea and through the Black Sea and which use the strategic position of Taranto for the entrance/dispatching of goods in Europe from the Far East and Suez-Gibraltar routes.
The platform will offer both storage and transport of goods services, so to rationalize the many phases and using competitive outsourcing as it usually is in other Mediterranean platforms; the near Container Terminal will allow us to guarantee a complete shipping and distribution cycle.
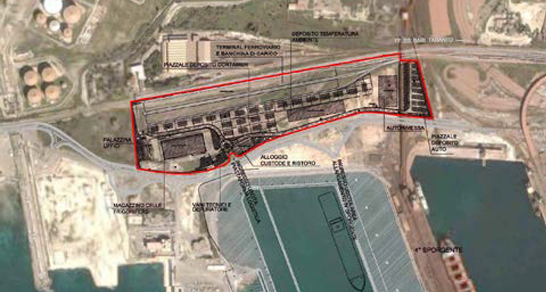
Buildings and plants serving the Logistic Platform
In regards to the different services offered, the platform will have:
– An offices building;
– An ambient temperature warehouse;
– A refrigerated warehouse;
– A keeper’s accommodation and resting facility;
– A garage.
The buildings have been planned considering the colors of the materials used, the different covering typologies and so to guarantee the operating necessities that the buildings must have. Following are some examples:
– adequate heights in order to allow the handling of goods;
– dimensions and overall number of the loading/unloading quays;
– restrictions in regards to number and dimensions of the windows;
– internal surface areas and volumes layout designed for the specific activities which will be carried out.
The main points of concern regarded the choice of the external covering typologies, material type, colors and technical solutions, the study of possible symmetrical solutions, the choice of specific details in order to uniform the different buildings, the outdoor design and planning of green areas.
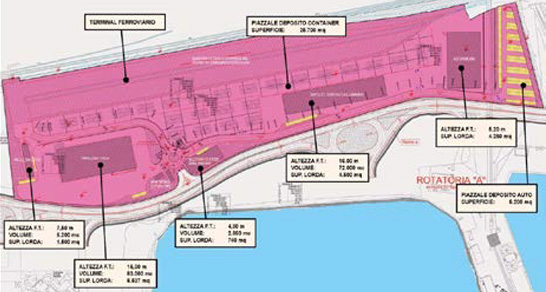
Offices building:
The new building will replace the pre-existing abandoned building once used by the maintenance team of RFI. The complete demolition and the creation of a new building is necessary in order to guarantee a new structure in compliance with seismic regulation’s standards. The new structure will have three floors (in addition to the the ground level) with a total surface of approximately 500 sq. m. per floor and a story height of about 3.3 m (room height of 2.86m, which become 2.7m if considering the dropped ceilings).
The total available surface is of about 1500 sq. m.
The visual perception will be improved by the use of brise soleil, which shall be mounted only along widows. The stairs and lift will be completely transparent.
The headwall which divides the two levels between the two longest facades of the building, will be covered with local rocks, while plant racks will be lined along the entire perimeter (they will be prefabricated elements in cls. with appropriate finishing) so to create a green element which shall “conceal” the new structures and infrastructures.
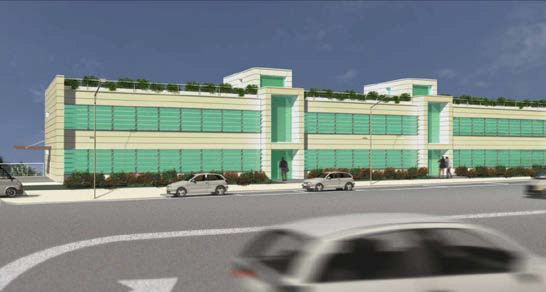
Warehouses:
The platform’s warehouses may be of two types, either at ambient temperature or refrigerated:
– Ambient temperature warehouse: the warehouse has a rectangular layout and the longest side is 156.1 m long, the shortest one is 31.3 m long, for a total surface area of about 4500 sq. m, 12.00 m high and the loading quay will be at -1,20m below ground level.
Refrigerated warehouse:
This building has been designed for the storage of perishable goods, has a rectangular layout with the longest side 113.5m long (external perimeter) and the shortest side 49.4m long (external perimeter), for an overall surface area of about 5.500 sq. m. and a volume of about 48.000 m3.
The actual height is of 10.50 m, while the loading quay’s height will be of -1.20m below ground level.
The building is divided in four cells which may be kept at different temperatures ranging between -25°C and +5°C and will also include further rooms such as an engine room, a control room, a workshop, a truck’s reloading area, restrooms and lockers room, control box, drive-in compact shelves, horizontal transport systems, plant design, safety systems.
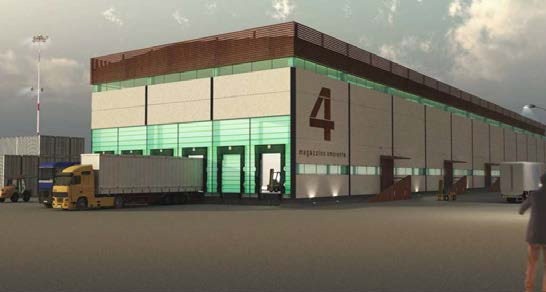
In order to change the uniformity of the high, plane and monochromatic buildings and in order to remedy to the fact that the two warehouses must be high and that the only windows present will be positioned in the offices and restroom floors, the following suggestions have been considered:
– use of a horizontal stripe so to avoid the closing panels to reach the ground and to create a contrast with the facades both in terms of color and surface type;
– use infill panels with horizontal openings and a grit finishing having the same color of the typical stones found in Puglia;
– the creation, above the first prefabricated panels level, where no windows are present, of a decorative line of windows so to uniform windows which have different dimensions.
– use of lined windows in the loading and unloading areas.
– the creation of lined windows on every building as a decorative element, which have been created using a panel which will conceal the roofing structure or the positioning of solar panels.
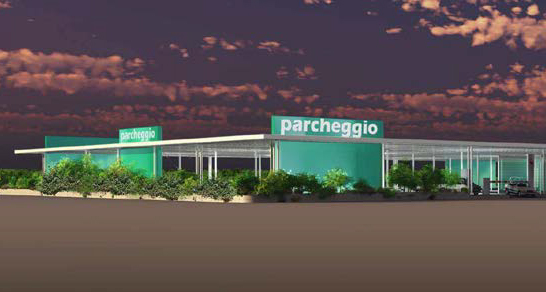
Indoor Garage:
This building is formed by a covered structure which will have a rectangular layout with the longest side 89.6 m long and the shortest one 54.6 m long, with a total surface area of approximately 4900 sq. m, 4.5m high and will be made with metal carpentry and besides being a vehicle deposit, it will also be equipped with a car wash system.
Behind the indoor garage and connected by already existent conveyors belts, an external vehicle deposit will also be created.
Decorative elements which will improve the overall appearance of the area, are plant racks which will be disposed around the entire perimeter and translucent closing panels displayed along the wind buttress, together with a specific structure made by small circular iron pillars.
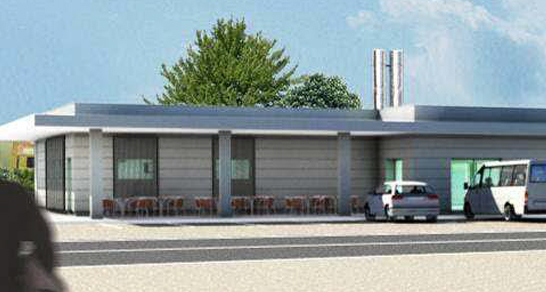
Keeper’s accommodation and resting facility:
The factory develops only on ground level with two sectors connected by a covering floor but divided by a colonnade so to have two distinct areas.
The first area will have a total surface of approximately 130 sq. m assigned to the keeper’s house with a near area of about 250 sq. m where control switchboards, control room, offices, archive, guardhouse will be based; the other area, will have a surface of about 120 sq. m used for the restrooms and 240 sq. m for the remaining resting facilities.
The building has a rectangular layout with the longest side 54.10 m long and the shortest 23.20 m long.
The resting facility area is equipped with a bar and a kitchen with 100 available seats if we consider 1.20m space for each person.
The external area will have different pavings depending on the function it will have (pedestrian area or parking area).
The wide glass windows of the lunch area and the smaller windows of the keeper’s accommodation, will all be similar thanks to steel nets, while the spaces between the lunchroom and the keeper’s house will be valued thanks to greenery.
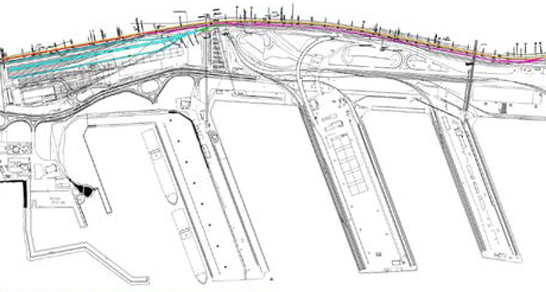
Railway terminal:
The railway terminal, which is inside the platform’s perimeter, is formed by four tracks which are used to keep the material transported by train during loading and unloading operations. Such tracks are 613.62 m, 584.74 m, 584.57 m and 650.44 m long.
Such tracks are equipped with Cogifer slot rails, brimmed so to allow the transit of wheeled vehicles on the tracks. The internal tracks will be separated from the external ones thanks to a gate which will also serve for possible customs necessities.
The terminal will be connected to the national railway system thanks to an already existing track, which is now part of a set of abandoned tracks and which will be only used for this specific purpose. Following the creation of adequate exchanging points and the updating of the just mentioned track, the terminal will be connected to the railway station of Taranto.
Due to the configuration of the railway station of Taranto, such connection will allow the arrival of maximum two trains each day, with a maximum length of 440m.
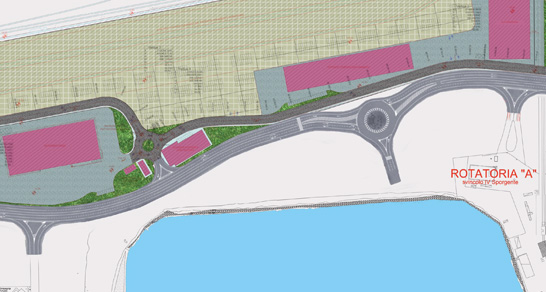
Container deposit area:
A container deposit area of 25,700 sq. m will also be created. The deposit will have a total of 480 container areas of 2,45 x 6,10 m and will have two separate and independent entrances/exits, so to facilitate the loading and unloading of goods. On the project, the hight is of +5.50 m which is the same for the entire deposit area and railway terminal.
Internal transit routes:
The transit routes inside the platform area, develop for approximately 750 m, have two lanes 3.75 m wide for each direction, with 1.5 m road shoulders and a 1.5 m sidewalk. At the entrance of the platform, a traffic circle will guarantee a better traffic flow.
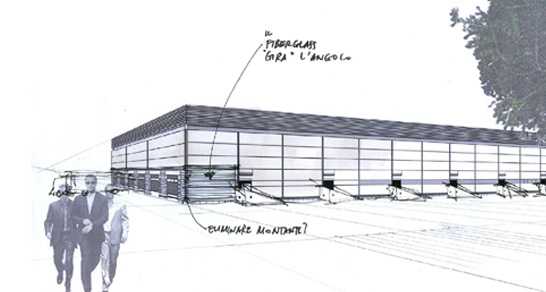
Plants:
Concerning with the creation of the platform, a series of plants will also be created:
– Switchboards/transformer room of the medium and low voltage system;
– Lightening system of the entire area and of the external perimeter (light towers 25 m high and poles 4.50 m high);
– Security systems equipped with video cameras, control room and security booth;
– Fire detection and extinguishing systems, including the storage tank;
– Drinkable water and sewer system;
– Wastewater treatment systems.
Parking areas:
Each building will have appropriate parking areas for employers and guests.
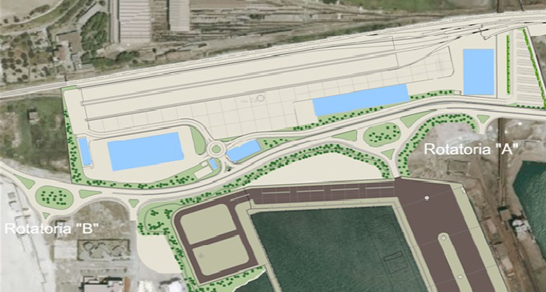
Planning of green spaces:
Visual camouflaging will be carried out by a natural and visual improvement of the area. Following the landscape architecture, the of the logistic platform which will be involved is given by the office buildings (urban) for which green spaces will be created in order to decorate the area with decorations which are usually used in urban sites.
The planning of green spaces comply to all traffic safety standards required. The actions regarding the camouflaging of the platform’s areas, all involve the creation of green areas following a specific layout. In regards to the plants to be used, the project establishes the use of both trees and bushes which respect the regional biodiversity of the area and guarantee a positive aesthetic outcome. The planning of green spaces also establishes the grassing of the entire area (of approximately 11,600 sq. m).